Introduction to Ready Mix Concrete
Ready-mix concrete (RMC) has transformed the construction industry by providing a fast, efficient, and reliable solution for various building projects. The ready-mix concrete is prepared in a batching plant, mixed to precise specifications, and then delivered directly to the job site, typically using transit mixers. This method ensures a consistent quality of concrete that can be customized for different applications, providing immense benefits over on-site concrete mixing.
In this comprehensive guide, we will explore everything you need to know about ready-mix concrete, including its types, applications, benefits, and best practices for ensuring a successful project. Whether you’re a homeowner, contractor, or property developer, understanding the ins and outs of RMC will help you make better decisions for your construction needs.
What is Ready Mix Concrete?
Ready-mix concrete is a specialized type of concrete that is mixed off-site in a controlled environment. It is delivered in a plastic state to construction sites in truck-mounted mixers. The composition includes cement, water, and aggregates like sand, gravel, or crushed stone, along with optional additives to enhance performance.
Types of Ready Mix Concrete
There are several types of ready-mix concrete to suit different construction applications:
- Standard Ready Mix Concrete: This is the most common type, delivered ready for general construction purposes.
- High-Strength Concrete: This type of RMC is designed to withstand high pressure and is often used in large infrastructure projects like bridges or tall buildings.
- Self-Compacting Concrete (SCC): SCC flows easily into tight spaces without the need for vibration, making it ideal for complex structural projects.
- Fiber-Reinforced Concrete: Fibers (steel, glass, or synthetic) are added to enhance the strength, durability, and crack resistance of the concrete.
- Accelerated Set Concrete: This type of concrete contains chemicals that speed up the curing process, ideal for projects on tight schedules.
Benefits of Using Ready Mix Concrete
Ready-mix concrete offers several advantages over traditional site-mixed concrete, both in terms of quality and efficiency. Here are some of the key benefits:
1. Consistency and Quality Control
One of the biggest advantages of ready-mix concrete is its consistent quality. Since the mixing is done in a controlled environment, there is less risk of human error or variation in the mix ratio. The batching plants use advanced computerized systems to ensure that the mix proportions meet the specified requirements, delivering a consistent product every time.
2. Time Efficiency
With ready-mix concrete, you eliminate the need to prepare concrete on-site. This can save significant time, particularly for large-scale construction projects. The concrete arrives ready to pour, allowing you to move quickly from delivery to placement.
3. Cost-Effectiveness
While the initial cost of RMC may seem higher than site-mixed concrete, its efficiency can lead to long-term savings. With fewer workers required for mixing and less material wastage, labor costs and material expenses are reduced.
4. Reduced Material Wastage
Since ready-mix concrete is mixed precisely to order, it helps in reducing material waste on construction sites. Additionally, there is no excess production of cement, which can contribute to a more sustainable construction process.
5. Versatility
Ready-mix concrete is highly customizable. Based on your project’s needs, you can choose different types of RMC with varying strengths, textures, and properties. This makes it suitable for a wide range of construction projects, from simple sidewalks to complex architectural structures.
6. Sustainability
Modern batching plants often incorporate eco-friendly technologies, such as recycling leftover materials and reducing water consumption. Using ready-mix concrete can also lower transportation and energy costs by delivering precise quantities without excess material.
Applications of Ready Mix Concrete
Ready-mix concrete is used in a wide variety of projects, from small residential buildings to large-scale infrastructure projects. Some common applications include:
1. Residential Buildings
Ready-mix concrete is widely used in the construction of homes, particularly for foundations, walls, driveways, and patios. Its consistency and strength make it ideal for building long-lasting, durable residential structures.
2. Commercial and Industrial Structures
For commercial buildings, warehouses, and factories, ready-mix concrete is often the go-to material. The high strength and durability required for industrial applications make RMC an excellent choice, particularly for floors, columns, and roofs.
3. Infrastructure Projects
Ready-mix concrete plays a crucial role in large infrastructure projects like bridges, highways, tunnels, and airports. High-strength and durable concrete types are typically used in these applications to ensure safety and longevity.
4. Architectural Concrete
RMC can be customized with color pigments and additives to create aesthetically pleasing architectural designs. It is commonly used in the construction of facades, sculptures, and decorative elements in modern buildings.
5. Precast Concrete Elements
Ready-mix concrete is often used in the production of precast elements like beams, columns, and panels, which are manufactured in factories and then transported to construction sites.
Best Practices for Using Ready Mix Concrete
To ensure a successful project, it’s essential to follow best practices when using ready-mix concrete. Below are some key tips:
1. Proper Planning and Scheduling
The timing of ready-mix concrete deliveries is crucial. Coordinate with your supplier to ensure that the concrete arrives at the correct time, particularly in large projects where delays can lead to concrete setting before it is poured.
2. Ensure Proper Equipment on Site
Before the concrete arrives, make sure you have the necessary equipment in place, such as concrete pumps, wheelbarrows, or cranes, depending on the size and location of your pour. This ensures quick and efficient placement.
3. Preparation of the Pouring Area
The area where the concrete will be poured should be properly prepared, cleaned, and reinforced if necessary. Any formwork or rebar should be in place and secured.
4. Monitor Weather Conditions
Extreme weather conditions, such as very hot or cold temperatures, can affect the concrete curing process. In cold weather, consider using additives to speed up the curing process. In hot weather, it may be necessary to cool the concrete or adjust the water content to prevent it from setting too quickly.
5. Curing the Concrete Properly
Proper curing is vital to the long-term strength and durability of the concrete. This can involve keeping the surface wet, using curing compounds, or covering the concrete with moist fabric to maintain appropriate moisture levels during the curing process.
Understanding the Delivery Process of Ready Mix Concrete
The ready-mix concrete delivery process involves several steps to ensure timely and efficient delivery:
Step 1: Ordering the Concrete
When ordering, provide accurate details about the project, including the type of concrete, quantity, and any specific requirements, such as additives or particular strength levels.
Step 2: Transportation
The concrete is transported in specialized trucks equipped with rotating drums that keep the mix in motion, preventing it from setting during transport.
Step 3: Site Arrival
Once the truck arrives at the site, the concrete can be discharged directly into the pour area, or pumped into place using a concrete pump.
Step 4: Pouring and Finishing
After pouring, the concrete should be leveled and finished to the desired smoothness or texture using tools like trowels and screeds.
Common Challenges with Ready Mix Concrete and How to Overcome Them
1. Delays in Delivery
Concrete begins to set within a limited time after mixing, typically within 90 minutes. To avoid delays, schedule deliveries carefully and ensure the site is ready for placement.
2. Inconsistent Quality
Although ready-mix concrete is known for consistency, incorrect ordering or poor communication can result in receiving the wrong mix. Always double-check the order and specifications with your supplier.
3. Weather-Related Issues
Extreme temperatures can affect the performance of the concrete. Consider using appropriate additives to control the setting time and curing process in different weather conditions.
4. Cracking After Placement
Cracking can occur due to improper curing, excessive water in the mix, or rapid drying. Ensure proper curing methods are used and avoid overwatering the mix.
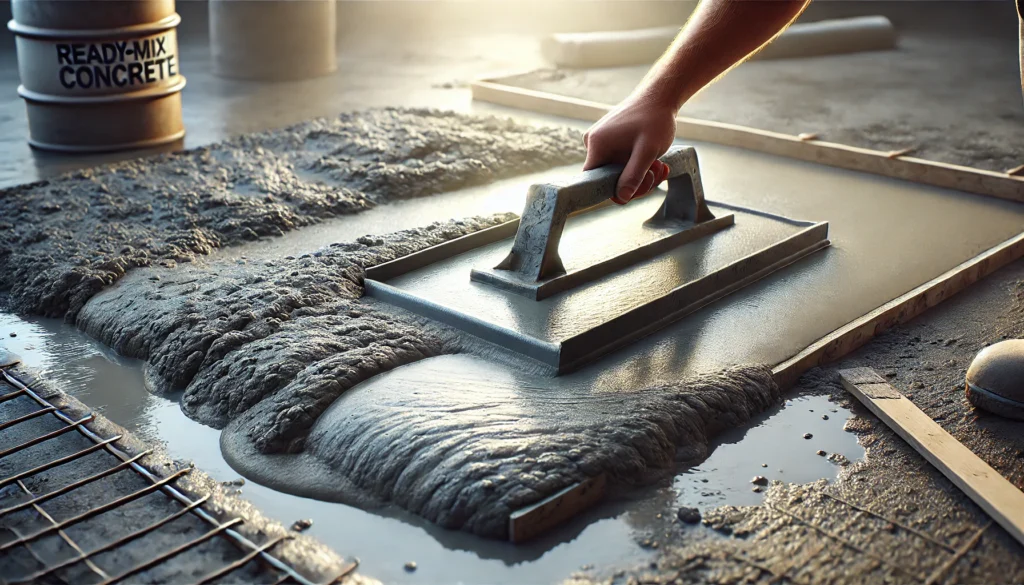
Ready Mix Concrete Industry in Malaysia
The ready-mix concrete (RMC) industry in Malaysia plays a crucial role in supporting the country’s construction sector, which is experiencing steady growth driven by both public and private infrastructure developments. This market has expanded due to increasing demand for efficient and high-quality building materials, particularly as the government continues to push forward with initiatives like urban infrastructure upgrades, large-scale transportation projects, and affordable housing.
Key Market Drivers
- Infrastructure Development: Malaysia’s ongoing investments in large-scale infrastructure projects, such as highways, airports, and rail networks, have spurred the growth of the ready-mix concrete market. These projects demand high volumes of concrete, with the RMC sector benefiting due to its consistency, quality control, and time-saving advantages.
- Urbanization and Residential Projects: Rapid urbanization in cities like Kuala Lumpur, Penang, and Johor Bahru has led to increased residential construction. Ready-mix concrete is often the material of choice for high-rise buildings, apartment complexes, and mixed-use developments, as it meets the need for high-strength, durable concrete in such projects.
- Sustainability Efforts: As environmental concerns grow, many RMC producers in Malaysia are adopting greener technologies, such as recycling excess concrete and utilizing eco-friendly additives. These practices not only reduce waste but also align with global sustainability trends, making the industry more attractive to environmentally conscious developers.
Industry Structure and Key Players
The ready-mix concrete market in Malaysia is quite fragmented, with both large multinational corporations and local firms competing. Major companies like Lafarge, Holcim, and Heidelberg Materials are prominent in the market, controlling a significant share of the total concrete supply. However, local players, many of whom are members of the National Ready-Mixed Concrete Association of Malaysia (NRMCA), also contribute significantly, supplying roughly 70% of the country’s total concrete consumption.
Challenges Facing the Industry
Despite its growth, the Malaysian RMC industry faces several challenges:
- Cost Pressures: Fluctuations in the prices of raw materials like cement, aggregates, and fuel can impact the cost structure of RMC companies. These rising costs are sometimes passed on to consumers, which can slow down project timelines.
- Quality Control: While RMC is known for its consistency, maintaining strict quality standards across different plants and suppliers remains a challenge. Continuous investment in technology and training is essential to ensure product quality.
- Skilled Labor Shortages: Like many construction-related industries, the RMC sector in Malaysia experiences a shortage of skilled labor, which can affect both production efficiency and overall project quality.
Future Outlook
Looking forward, the Malaysian ready-mix concrete market is expected to continue growing as infrastructure investments ramp up. The government’s focus on improving transportation networks and expanding affordable housing will provide a strong foundation for the industry’s expansion. Additionally, the trend towards smart cities and green building projects will likely drive innovation in the sector, with companies incorporating more sustainable practices in their operations.
Conclusion
Ready-mix concrete (RMC) has established itself as a crucial component of modern construction, offering numerous advantages such as improved quality control, efficiency, and reduced labor costs. Its versatility allows it to be tailored to various project needs, from residential housing to complex infrastructure. Globally, RMC continues to grow in popularity due to its consistent performance and alignment with sustainability efforts.
In Malaysia, the RMC industry plays a pivotal role in the country’s development. With urbanization and large infrastructure projects on the rise, the demand for ready-mix concrete is expected to continue growing. The industry, supported by key players and local organizations like the National Ready-Mixed Concrete Association of Malaysia (NRMCA), supplies the majority of the nation’s concrete needs. However, challenges such as fluctuating raw material costs and labor shortages persist.
As the Malaysian government continues to push forward with infrastructure and affordable housing projects, the RMC market will likely see continued expansion. By adopting advanced technologies and sustainable practices, the industry is poised to meet the growing demands of the construction sector while maintaining high standards of quality and environmental responsibility.
In summary, ready-mix concrete not only offers technical and logistical benefits but is also a key driver of Malaysia’s construction sector, supporting the nation’s vision of modern urbanization and development.
Pro Inspect Solution: Your Trusted Partner for Building Inspection
If you’re involved in a construction project in Malaysia, ensuring the structural integrity of your work is crucial. Pro Inspect Solution offers a range of property and building inspection services, including structural assessments, which are vital for ensuring that the quality of the concrete and other materials used meet the highest standards.
Visit Pro Inspect Solution for comprehensive inspection services and protect your investment with professional oversight.
FAQ on Ready Mix Concrete
What is meant by ready mix concrete?
Ready-mix concrete (RMC) is concrete that is prepared off-site in a specialized batching plant according to precise specifications. It is then transported to the construction site in a transit mixer truck in a plastic (fluid) state. This method ensures consistent quality and reduces the need for on-site mixing.
What is the difference between concrete mix and ready mix?
The key difference between concrete mix and ready-mix concrete is in the preparation process. Concrete mix is prepared on-site by mixing raw materials like cement, water, and aggregates. In contrast, ready-mix concrete is pre-mixed off-site in a controlled environment and delivered ready to pour. Ready-mix ensures consistency and quality control, whereas on-site mixing can be subject to variations in quality.
What is the difference between dry mix and ready mix concrete?
Dry mix concrete consists of cement and aggregates that are mixed dry, with water added later at the job site. It requires mixing at the site before being placed. Ready-mix concrete, on the other hand, is pre-mixed with water in a batching plant and delivered in a ready-to-use state, saving time and ensuring consistency.
What is the use of ready mix concrete?
Ready-mix concrete is used in a wide variety of construction applications, including residential buildings, commercial structures, highways, bridges, and large infrastructure projects. Its versatility, strength, and durability make it suitable for both structural and decorative elements, as well as large-scale urban development projects.
Why is ready mix concrete better?
Ready-mix concrete is considered superior due to several reasons:
- Consistency: It is mixed in a controlled environment, reducing the chances of error in mixing proportions.
- Time Efficiency: It is delivered ready to pour, eliminating the need for on-site mixing and saving labor and time.
- Cost-Effective: Reduced material wastage and lower labor costs make it an economically efficient choice, especially for large projects.
- Quality Control: Batching plants use advanced technology to ensure precise mixing ratios, resulting in higher quality and more durable concrete.
What are the disadvantages of ready mix concrete?
While ready-mix concrete has many advantages, there are a few disadvantages to consider:
- Transportation Costs: For remote locations, transportation can be expensive, and the concrete may begin to set before it arrives at the site.
- Limited Work Time: Once mixed, ready-mix concrete must be used quickly, usually within 90 minutes, before it begins to harden.
- Initial Cost: Ready-mix concrete can have a higher initial cost compared to site-mixed concrete, though the long-term savings often outweigh this.