Enhancing Construction Quality in Malaysia: A Guide to CIDB and QLASSIC Standards
The construction industry in Malaysia is undergoing a significant transformation, driven by the efforts of the Construction Industry Development Board (CIDB) and the implementation of the Quality Assessment System in Construction, commonly known as QLASSIC. This guide will explore the role of CIDB, the importance of QLASSIC, and the critical role of property inspections in ensuring construction quality.
Understanding CIDB and QLASSIC
The Construction Industry Development Board (CIDB) Malaysia is the cornerstone of the nation’s construction industry, providing regulation and strategic direction. Established under the Construction Industry Development Board Act (Act 520) in 1994, CIDB’s mission is to enhance the quality and standards within the construction sector, ensuring that Malaysian projects align with global best practices.
One of CIDB’s flagship initiatives is QLASSIC, a standardized system designed to evaluate and certify the workmanship quality of construction projects. QLASSIC provides an independent, objective assessment of the construction quality based on approved specifications and standards. For developers and contractors, adhering to QLASSIC standards is more than a regulatory requirement; it is a commitment to delivering superior quality, enhancing customer satisfaction, and building trust with stakeholders.
Why Property Inspections Matter
Property inspections are vital to maintaining high standards in construction. They serve as a critical checkpoint to identify potential defects and ensure compliance with QLASSIC standards. Regular inspections not only prevent costly repairs down the line but also enhance the market value of the property by assuring buyers of its quality and safety.
Adherence to CIDB’s QLASSIC standards during inspections provides a benchmark for quality assurance, offering peace of mind to all parties involved. Properties that undergo thorough inspections and meet QLASSIC criteria often enjoy higher demand, reflecting the value of consistent quality control.
Key Types of Property Inspections
Property inspections, as outlined by CIDB under QLASSIC, can be categorized into three main stages: pre-construction, in-progress, and final inspections. Each stage plays a unique role in ensuring that construction quality meets the highest standards.
1. Pre-Construction Inspections:
These inspections ensure that the site is ready for construction, focusing on compliance with design plans, legal approvals, and environmental assessments. By addressing potential issues early, pre-construction inspections help prevent delays and costly modifications.
2. In-Progress Inspections:
Conducted at various stages throughout the construction process, in-progress inspections verify that work is proceeding according to plan. These inspections cover critical aspects such as structural integrity, material quality, and system installations, ensuring that the construction adheres to QLASSIC standards.
3. Final Inspections:
Final inspections are the last checkpoint before a property is handed over. They ensure that the finished project meets all quality benchmarks, from aesthetics to functionality. Passing this inspection is crucial for obtaining QLASSIC certification, which signifies that the property is built to the highest standards.
Advanced Inspection Techniques and Tools
Modern property inspections have evolved beyond traditional methods, incorporating advanced technology to enhance accuracy and efficiency. Some of the key techniques and tools include:
- Non-Destructive Testing (NDT): Methods like ultrasonic testing and ground-penetrating radar allow inspectors to assess structural integrity without damaging the building.
- Material Testing: Tools such as the rebound hammer test for concrete and tensile strength tests for steel ensure that materials meet the required standards.
- Drone Inspections: Drones provide access to hard-to-reach areas, capturing high-resolution images for detailed analysis, particularly useful for inspecting roofs and high elevations.
- Infrared Cameras: These devices detect thermal anomalies, identifying potential issues like moisture intrusion or insulation deficiencies that are not visible to the naked eye.
The integration of these technologies ensures that inspections are thorough, identifying defects early and safeguarding the quality and longevity of the structure.
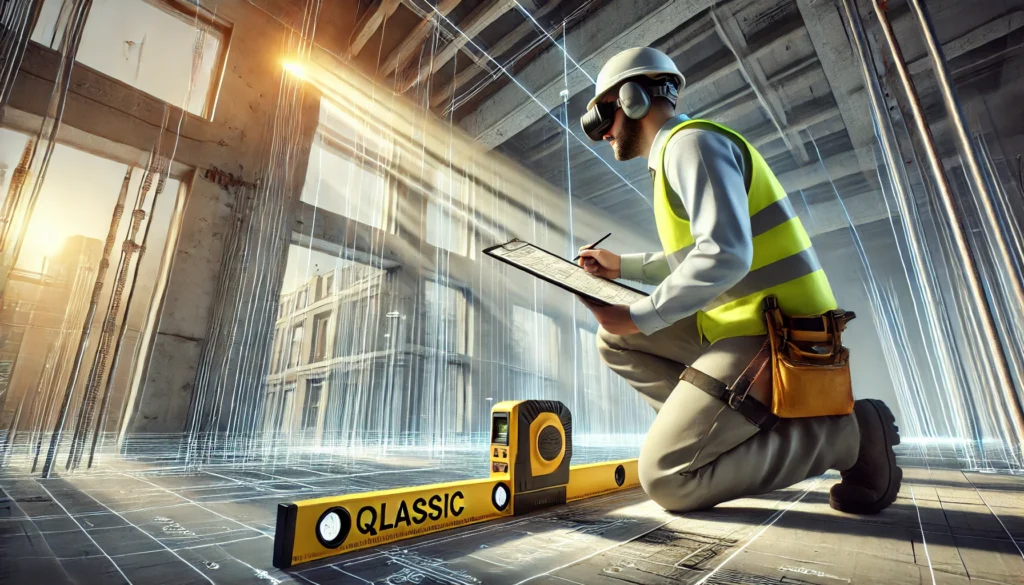
The QLASSIC Assessment Process
The QLASSIC assessment process is a comprehensive procedure that ensures construction projects meet CIDB’s stringent quality standards. Here’s a breakdown of how the process works:
- Scheduling and Preparation:
The process begins with scheduling an assessment through CIDB. Proper site preparation and the availability of necessary documents are crucial to a smooth inspection. - Inspection Procedure:
Trained assessors evaluate various components of the construction, using a standardized checklist based on QLASSIC criteria. This ensures a thorough and unbiased assessment. - Scoring and Documentation:
Each element is scored, and these scores are aggregated to produce an overall quality score. A detailed report is generated, highlighting areas of compliance and those needing improvement.
Adhering to this process not only helps construction projects achieve high QLASSIC scores but also reinforces the commitment to quality excellence.
Common Defects Identified During Inspections
During property inspections, several common defects are often identified, which can significantly impact the quality and safety of a property:
- Structural Integrity Issues: Cracks in walls, floors, and ceilings, or signs of uneven settling, can indicate foundational problems.
- Finishing Defects: Poor paint application, uneven plastering, and misaligned tiles are common issues that affect the property’s aesthetic and durability.
- Electrical and Plumbing Problems: Faulty wiring, leaks, and non-compliant installations are serious defects that require immediate attention.
- Safety Concerns: Inadequate fire safety measures and improper emergency exits are critical safety defects that must be addressed to ensure occupant safety.
Identifying and addressing these defects early is crucial for maintaining the property’s quality and ensuring it meets QLASSIC standards.
Best Practices for Passing QLASSIC Inspections
To ensure that your property passes QLASSIC inspections, it’s essential to adopt a strategic approach that includes:
- Rigorous Quality Control: Implementing strict quality control measures throughout the construction process ensures compliance with QLASSIC standards.
- Use of High-Quality Materials: Ensuring that all materials meet required standards reduces the risk of defects and enhances the likelihood of passing inspections.
- Training and Education: Providing construction workers with comprehensive training on QLASSIC standards ensures that everyone involved is equipped to meet these requirements.
- Consulting Experts: Engaging with QLASSIC experts or hiring a dedicated coordinator can provide valuable insights and ensure best practices are followed.
By following these best practices, construction projects can achieve high QLASSIC scores, enhancing their marketability and stakeholder trust.
Future Trends in Property Inspections
As the construction industry evolves, so too does the field of property inspections. Emerging technologies such as Artificial Intelligence (AI) and smart building systems are set to revolutionize how inspections are conducted. AI tools can analyze vast amounts of data quickly, identifying potential issues and suggesting maintenance actions before problems arise. Smart sensors embedded in buildings provide real-time monitoring of structural conditions, allowing for proactive maintenance and reducing the need for manual inspections.
These advancements will likely be integrated into QLASSIC standards, creating more dynamic and flexible assessment criteria that reflect the latest in construction technology and quality management. Staying ahead of these trends will be crucial for industry stakeholders looking to maintain high standards and drive innovation in construction quality.