Concrete is the foundation of modern construction, but when it comes to choosing the right method for a project, the debate between precast concrete and traditional concrete (cast-in-place) is common. Both methods have their merits and are suited to different types of projects, but the choice depends on factors like budget, timeline, structural needs, and environmental impact.
In this blog, we will explore the differences between precast concrete and traditional concrete in terms of production, installation, costs, and suitability for various applications. By the end, you’ll have a clearer understanding of which method is better for your project.
What is Precast Concrete?
Precast concrete refers to concrete elements that are manufactured in a controlled factory environment and then transported to the construction site for installation. Precast components, such as beams, columns, slabs, and panels, are produced in molds and subjected to rigorous quality control before being delivered to the job site.
Advantages of Precast Concrete
- Quality Control: Since precast concrete is made in a factory setting, there is greater control over material quality, curing conditions, and production processes. This ensures consistent and high-quality components.
- Faster Construction: Precast components can be manufactured while site preparation is still underway. Once the components are ready, they are simply assembled on-site, reducing the time spent on construction.
- Durability: Precast concrete elements are often more durable than cast-in-place concrete due to better curing conditions and optimized reinforcement designs.
- Less Weather Dependency: Because precast concrete is produced off-site, weather conditions like rain or extreme temperatures do not affect the production process. This can help avoid construction delays.
- Sustainability: Precast factories often have more efficient use of materials, producing less waste. Many precast elements can be made from recycled materials, contributing to greener building practices.
What is Traditional Concrete?
Traditional concrete (or cast-in-place concrete) is poured, molded, and cured directly on the construction site. The formwork is built on-site, and once the concrete is poured, it needs time to cure before the next construction steps can proceed.
Advantages of Traditional Concrete
- Flexibility on Site: Traditional concrete allows for greater flexibility on-site, especially if last-minute adjustments or design changes are needed. The molds can be adjusted or moved to meet specific site requirements.
- Lower Initial Costs: While it might take longer to install, traditional concrete can have lower upfront material and transportation costs compared to precast elements.
- No Size Limitations: With cast-in-place concrete, there are no limitations to the size or shape of the structure. Large monolithic structures are easier to execute with cast-in-place methods.
- Ideal for Custom Designs: If your project requires intricate or custom designs that need to be built on-site, traditional concrete offers more flexibility in design and formwork.
Key Differences Between Precast Concrete and Traditional Concrete
1. Production Process
- Precast Concrete: Manufactured off-site in a controlled environment, which allows for better quality assurance, uniformity, and precision.
- Traditional Concrete: Mixed and poured on-site, making it subject to environmental conditions and potential inconsistencies.
2. Speed of Construction
- Precast Concrete: Offers faster construction times since the components are pre-made and can be installed as soon as the site is ready.
- Traditional Concrete: Requires more time due to the need for on-site mixing, pouring, and curing, which can extend project timelines.
3. Cost Considerations
- Precast Concrete: While precast concrete can have higher initial production costs due to the need for molds and transportation, it often results in savings in the long run thanks to reduced labor and faster project completion.
- Traditional Concrete: Initially more affordable, especially for small-scale projects. However, long construction times and potential delays can increase labor and overhead costs.
Factor | Precast Concrete | Traditional Concrete |
---|---|---|
Production | Made off-site, in controlled environments | Mixed and poured on-site |
Construction Time | Faster, as components arrive ready for assembly | Slower, requires curing on-site |
Cost | Higher upfront, but potential long-term savings | Lower initial cost, but higher labor expenses |
Weather Dependency | Minimal impact from weather conditions | Prone to delays due to weather |
Flexibility | Less flexible for on-site adjustments | High flexibility for site-specific customization |
Durability | Often more durable due to controlled curing | Depends on on-site curing conditions |
When to Choose Precast Concrete
Precast concrete is particularly advantageous for projects that prioritize speed, quality control, and durability. Here are some scenarios where precast concrete is the best choice:
- Time-Sensitive Projects: Since precast elements are manufactured ahead of time, installation on-site is much quicker. This makes precast ideal for projects with tight deadlines.
- Repetitive Structural Elements: In projects like multi-story buildings or parking garages where the same structural elements (like beams and columns) are used repeatedly, precast concrete allows for efficient mass production.
- Infrastructure Projects: Bridges, tunnels, and large-scale infrastructure projects benefit from precast concrete’s precision and durability. It reduces disruption to roadways and other public areas during installation.
- Weather-Resistant Construction: Precast concrete is less affected by adverse weather conditions, ensuring that the project remains on schedule even in challenging climates.
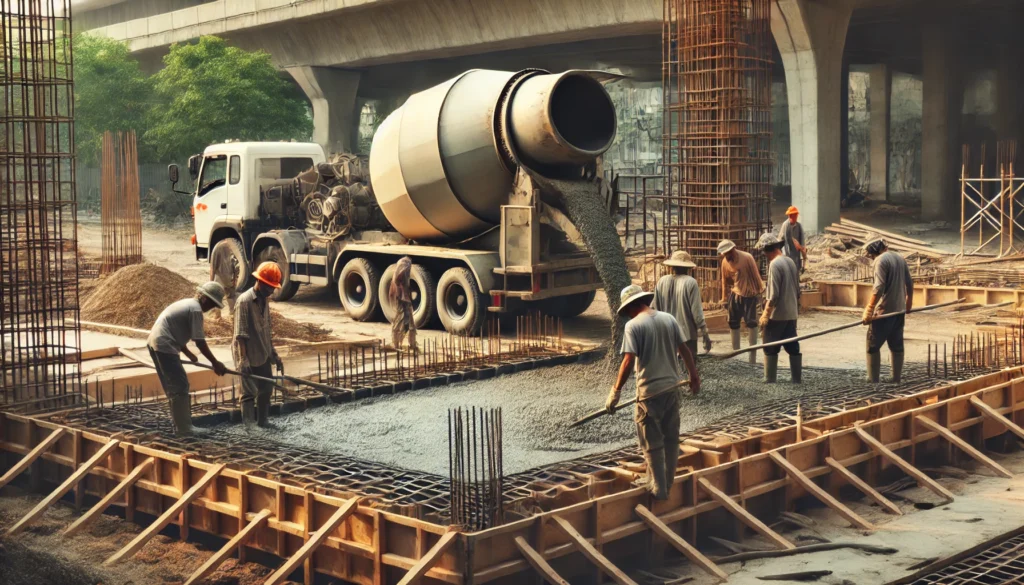
When to Choose Traditional Concrete
While precast concrete has numerous benefits, traditional cast-in-place concrete is better suited for certain types of projects, such as:
- Complex, Custom Designs: If the project requires intricate or unique architectural designs that need to be created on-site, traditional concrete offers more flexibility.
- Budget-Constrained Projects: For smaller-scale projects with limited budgets, traditional concrete might be a more cost-effective solution in terms of material and transportation costs.
- Monolithic Structures: If a large, continuous pour of concrete is required for the structural integrity of a building or other structure, traditional concrete can provide the necessary cohesion.
- Remote Locations: Projects in remote areas where transporting large precast elements would be costly or logistically challenging might benefit from using cast-in-place methods.
Environmental Impact of Precast vs. Traditional Concrete
Sustainability is increasingly a concern in construction, and both precast and traditional concrete have different environmental footprints. Precast concrete often generates less waste because it is made in controlled environments, where the exact amount of material needed is used, and excess can be recycled. Precast components also often have a longer lifespan due to improved quality control, reducing the need for repairs and replacements.
On the other hand, traditional concrete may have higher wastage due to the variability of on-site conditions. However, recent innovations in concrete technology, such as the use of low-carbon concrete and recycled aggregates. It helping to reduce the environmental impact of both methods.
Conclusion
Both precast concrete and traditional concrete have their place in the construction world. The decision between the two comes down to the specific needs of your project. Precast concrete is ideal for projects that require speed, precision, and durability, especially in repetitive or large-scale structures. Traditional concrete offers greater flexibility and is often more cost-effective for smaller, custom projects.
To make the right decision, consider factors like budget, timeline, design complexity, and site conditions. A detailed cost-benefit analysis can also help determine which method aligns better with your project’s goals.
Frequently Asked Questions (FAQs)
1. Is precast concrete more expensive than traditional concrete?
Precast concrete can have higher initial costs due to production and transportation. But it often resulted in overall savings thanks to faster installation and reduced labour costs.
2. Can precast concrete be used for residential buildings?
Yes, precast concrete is increasingly being used in residential projects for walls, floors, and even complete modular homes due to its durability and energy efficiency.
3. How long does precast concrete last?
Precast concrete is known for its durability and can last for decades with minimal maintenance. Its controlled manufacturing process results in higher-quality components compared to traditional concrete.
4. Is traditional concrete better for complex designs?
Yes, traditional cast-in-place concrete offers more flexibility for complex and custom designs. It also makes it a preferred choice for projects that require intricate on-site adjustments.
5. What are the environmental benefits of using precast concrete?
Precast concrete typically generates less waste during production and can incorporate recycled materials. Its durability also reduces the need for repairs, which lowers the overall environmental impact over time.