Reinforced concrete is one of the most widely used construction materials due to its durability, versatility, and ability to bear substantial loads. However, despite its strength, reinforced concrete can deteriorate over time due to factors such as environmental exposure, structural stresses, or poor-quality materials. Regular reinforced concrete inspections are critical to identifying issues before they become significant safety hazards, ensuring structural integrity and prolonging the lifespan of the structure.
In this blog post, we will explore everything you need to know about reinforced concrete inspections. From understanding the importance of these inspections to learning the detailed steps involved in the process, we’ll cover it all. Whether you are a property owner, a contractor, or an engineer, this guide will provide valuable insights into reinforced concrete inspection best practices.
Why Is Reinforced Concrete Inspection Important?
Reinforced concrete (RC) structures, whether buildings, bridges, or foundations, play a crucial role in modern infrastructure. Over time, various factors such as environmental conditions, mechanical loads, and material quality can affect the performance and safety of these structures. Regular inspections of reinforced concrete help to:
- Ensure Structural Integrity: Inspections detect early signs of damage such as cracks, corrosion, or deflections, preventing catastrophic failures.
- Prevent Costly Repairs: Timely detection of issues allows for minor repairs that can be far less expensive than addressing major structural problems.
- Extend the Lifespan of Structures: Well-maintained structures can last much longer with proper inspections and maintenance schedules.
- Comply with Regulations: Many regions require regular inspections to meet building safety codes, especially in seismic or harsh environmental zones.
Common Causes of Concrete Deterioration
Before diving into the inspection process, it’s important to understand the main causes of concrete deterioration. Recognizing these factors will help you better understand what to look for during an inspection.
1. Corrosion of Reinforcement Steel
Reinforcement steel, often embedded in concrete, can corrode due to exposure to moisture, salt (common in coastal or road environments), or carbonation. This corrosion leads to expansion of the steel, cracking, and eventual failure of the concrete.
2. Freeze-Thaw Cycles
Concrete in colder climates is subject to freeze-thaw cycles. Water trapped in the pores of the concrete expands when frozen, which can lead to cracking and spalling over time.
3. Chemical Attack
Certain chemicals, such as sulfates in soil or water, can attack concrete and cause it to weaken. Chemical reactions can degrade both the concrete and the embedded steel.
4. Overloading
Concrete structures that bear loads beyond their design capacity can develop cracks or fail altogether. Continuous overloading accelerates the deterioration process.
5. Shrinkage Cracking
Shrinkage can occur during the curing process if the concrete dries too quickly. This can result in small, fine cracks on the surface, which may expand over time if not addressed.
6. Poor Construction Practices
Low-quality materials, improper mixing ratios, or inadequate curing can all contribute to premature deterioration. Proper supervision and quality control during construction are critical to preventing these issues.
Standards and Guidelines for Concrete Inspections
To maintain consistency and safety, reinforced concrete inspections follow various industry standards and guidelines. Some of the most important codes include:
- ACI 318: The American Concrete Institute (ACI) provides comprehensive standards for the design and construction of reinforced concrete structures.
- BS 8110: A British Standard covering structural use of concrete, focusing on design, material properties, and workmanship.
- ISO 1920: This international standard outlines test methods and procedures for evaluating concrete’s mechanical and physical properties.
- Eurocode 2 (EN 1992): A set of European guidelines governing the design of concrete structures.
These standards ensure that inspections are performed consistently and are based on established engineering principles.
Types of Reinforced Concrete Inspections
Reinforced concrete inspections can be divided into three main categories based on their purpose and frequency:
1. Visual Inspections
Visual inspections involve a detailed examination of the surface for visible signs of damage like cracks, spalling, discoloration, or water intrusion. These inspections can be conducted regularly, such as annually or biannually.
2. Non-Destructive Testing (NDT)
Non-destructive testing methods assess the internal condition of concrete without damaging the structure. Techniques like ultrasonic pulse velocity, ground-penetrating radar (GPR), and infrared thermography are commonly used for detailed analysis.
3. Destructive Testing
Destructive testing involves extracting core samples or drilling into the concrete to test the material’s properties in a lab. While invasive, this type of testing provides the most accurate data on the structure’s strength and durability.
The Reinforced Concrete Inspection Process: Step-by-Step Guide
The inspection process for reinforced concrete typically follows a structured approach to ensure thorough assessment. Here is a step-by-step guide:
Step 1: Preliminary Assessment
Before the actual inspection, gather all the necessary documents such as construction drawings, past inspection reports, and repair records. This helps in understanding the structure’s history and known issues.
Step 2: Visual Examination
Begin with a detailed visual inspection. Look for visible signs of distress, including cracks, corrosion of rebar, spalling, and water leakage. Document all findings with photographs.
Step 3: Non-Destructive Testing (NDT)
Depending on the initial findings, use NDT methods to investigate areas where internal damage may exist. Common methods include:
- Ultrasonic Testing: Evaluates the thickness and uniformity of the concrete.
- Ground-Penetrating Radar (GPR): Locates embedded reinforcement, voids, and defects within the concrete.
- Infrared Thermography: Detects moisture intrusion and delamination.
Step 4: Destructive Testing (if necessary)
If necessary, perform destructive testing by extracting core samples to test in a lab. This provides crucial data on compressive strength, carbonation depth, and chloride content.
Step 5: Data Analysis and Reporting
Analyze the data collected during the inspection. Provide detailed findings in an inspection report, which should include recommendations for repair or further testing if required.
Testing Methods for Reinforced Concrete Inspection
Several testing methods can be used to evaluate reinforced concrete structures. The most common methods include:
1. Rebound Hammer Test
A rebound hammer measures the surface hardness of the concrete and provides an estimate of compressive strength.
2. Ultrasonic Pulse Velocity (UPV)
UPV is a non-destructive test that measures the speed of sound waves through the concrete. It’s useful for detecting cracks, voids, and changes in material density.
3. Ground Penetrating Radar (GPR)
GPR is used to locate reinforcement bars, voids, and defects within concrete. It provides detailed imaging of the internal structure without the need for invasive drilling.
4. Carbonation Testing
Carbonation testing determines the depth of carbonation in concrete, which can affect the alkalinity of the concrete and lead to corrosion of reinforcement steel.
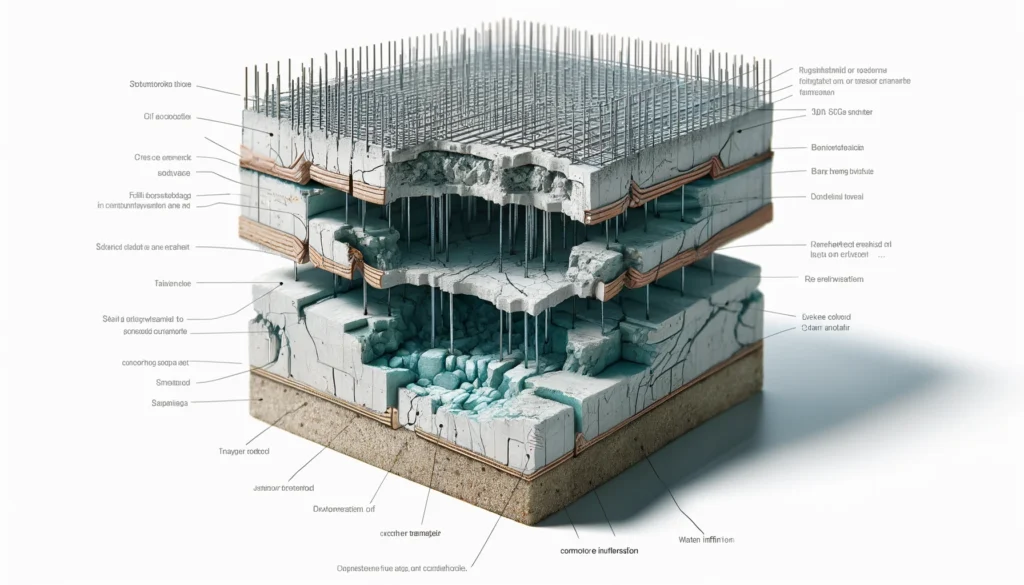
How to Interpret Inspection Results
Understanding the results of a reinforced concrete inspection requires expertise in structural engineering and material science. However, key factors to consider include:
- Crack Width: Larger cracks may indicate serious structural issues, while hairline cracks are often normal in reinforced concrete.
- Rebar Condition: Corrosion of rebar is a significant concern and requires immediate attention.
- Concrete Strength: Results from compressive strength tests should meet the original design specifications.
- Moisture Levels: High levels of moisture indicate potential water intrusion issues, which can lead to corrosion and cracking over time.
Repair and Maintenance Strategies for Reinforced Concrete
After inspection, the next step is to address any issues identified. Some common repair and maintenance strategies for reinforced concrete include:
- Crack Injection: For small to moderate cracks, epoxy or polyurethane injections can be used to seal the cracks and prevent water intrusion.
- Rebar Replacement: If reinforcement bars are corroded, they may need to be replaced or treated with corrosion inhibitors.
- Surface Coating: Applying a protective coating can prevent further moisture intrusion and slow down the deterioration process.
- Patch Repairs: Spalling or delamination can be addressed by patching the affected area with fresh concrete or mortar.
Pro Inspect Solution’s Role in Ensuring Structural Integrity
For professional reinforced concrete inspection services, Pro Inspect Solution is a trusted partner in Malaysia. They offer comprehensive building and structural assessment services, specializing in the inspection, testing, and evaluation of reinforced concrete structures. Their experienced team uses state-of-the-art tools and techniques to ensure your structures remain safe, durable, and compliant with local regulations.
Whether you are managing a residential property, an industrial facility, or a large infrastructure project, Pro Inspect Solution can provide you with expert guidance and reliable inspection reports.
Frequently Asked Questions (FAQs)
1. How to inspect reinforced concrete?
Inspecting reinforced concrete involves a combination of visual assessment and testing methods. The process typically begins with a visual inspection, looking for surface cracks, spalling, discoloration, or signs of moisture intrusion. Non-destructive testing (NDT) methods, such as ultrasonic pulse velocity (UPV), ground-penetrating radar (GPR), or infrared thermography, are then used to assess the internal condition of the concrete and detect hidden issues like voids, cracks, or rebar corrosion.
2. How do you test reinforced concrete?
Reinforced concrete can be tested through several methods, depending on the information needed. The most common tests include:
- Rebound Hammer Test for surface hardness.
- Ultrasonic Pulse Velocity (UPV) for internal defects and uniformity.
- Core Testing, where a sample of concrete is extracted and tested for compressive strength in a laboratory.
- Ground Penetrating Radar (GPR) for locating rebar and detecting voids or delamination.
Each test provides valuable information about the structural integrity and durability of the reinforced concrete.
3. How do you inspect rebar in concrete?
Rebar inspection involves both visual and non-destructive testing methods. A visual inspection looks for any signs of exposed or corroded rebar, typically through cracks or spalling in the concrete. Non-destructive methods such as GPR or electromagnetic cover meters are used to locate the rebar and measure its depth and spacing without damaging the structure. In cases where corrosion is suspected, further tests like half-cell potential measurements or extracting a sample may be performed to assess the condition of the rebar.
4. How do you inspect a concrete slab?
A concrete slab inspection starts with a thorough visual check for surface damage like cracks, spalling, or discoloration, which can indicate underlying issues. Non-destructive tests such as GPR can be used to assess the internal integrity of the slab, detect voids, or locate reinforcement bars. Additionally, moisture meters can help identify any water intrusion that might be compromising the slab’s durability. Depending on the findings, core samples might be taken for compressive strength testing.
5. How to check reinforcement bar quality?
Reinforcement bar quality can be checked by:
- Dimensional Inspection: Ensuring the rebar meets the design specifications for diameter and length.
- Tensile Strength Testing: Verifying the bar’s ability to withstand the required load.
- Corrosion Assessment: Visual inspection or tests like half-cell potential measurements to check for corrosion.
- Bend Test: Ensuring the rebar can bend without breaking or cracking, meeting ductility requirements.
It’s important that all rebars conform to the relevant standards such as ASTM, ISO, or local codes.
6. What are the criteria for rebar inspection?
Key criteria for rebar inspection include:
- Correct Diameter and Spacing: Ensuring the rebar size and spacing match the design specifications.
- Corrosion Resistance: Rebars should not show signs of rust or corrosion that could affect structural performance.
- Proper Alignment: Rebars should be placed according to the engineering design, ensuring proper alignment and cover within the concrete.
- Anchorage and Lapping: Rebars must have sufficient overlap or anchorage to transfer loads effectively.
- Cleanliness: Rebars should be free from contaminants like oil, mud, or excessive rust, which could interfere with bonding to the concrete.