Structural cracks in buildings are a common concern for both engineers and property owners. These cracks can indicate a variety of underlying issues, from minor cosmetic problems to significant structural damage. Understanding the causes of these cracks, how to assess them, and the appropriate methods for repair is crucial for maintaining the integrity and safety of any building.
In this comprehensive guide, we’ll explore the different types of structural cracks, the common causes, the assessment process, and the methods and materials used for repair according to the EN 1504 standards. We’ll also include a flow chart and table to help visualize the repair process.
Types of Structural Cracks
Structural cracks can manifest in various forms, and identifying the type of crack is the first step in addressing the problem. The most common types include:
- Vertical Cracks: Often found in walls, these cracks can indicate settlement issues or differential movement between building elements.
- Horizontal Cracks: Typically more concerning, horizontal cracks can suggest serious structural issues such as excessive load or foundation movement.
- Diagonal Cracks: Often caused by foundation settlement or seismic activity, these cracks run at an angle and can vary in severity.
- Stair-Step Cracks: Common in brick walls, these cracks follow the mortar lines in a step-like pattern, usually indicating foundation movement or settlement.
- Hairline Cracks: Fine cracks that are usually cosmetic but can widen over time, potentially leading to more serious issues.
Causes of Structural Cracks
Understanding the causes of structural cracks is essential for determining the appropriate repair method. Common causes include:
- Foundation Settlement: Differential settlement can cause uneven stress distribution, leading to cracks.
- Thermal Expansion and Contraction: Temperature fluctuations can cause materials to expand and contract, leading to cracking over time.
- Moisture Infiltration: Water penetration can weaken concrete and masonry, causing cracking and even structural failure.
- Load Stress: Excessive loads, either static or dynamic, can exceed the structural capacity of a building, leading to cracks.
- Seismic Activity: Earthquakes and other seismic events can cause significant cracking due to the sudden and violent movement of the earth.
- Corrosion of Reinforcement: When steel reinforcement corrodes, it expands, creating internal pressure that can crack the surrounding concrete.
Assessment of Structural Cracks
Before proceeding with repairs, a thorough assessment of the cracks is necessary. This involves:
- Visual Inspection: Identify the location, length, width, and pattern of the cracks.
- Monitoring: Use crack monitors or tell-tales to observe the progression of the cracks over time.
- Non-Destructive Testing (NDT): Techniques such as ultrasound, radar, or infrared thermography can detect internal defects without damaging the structure.
- Material Testing: Analyze core samples of the concrete or masonry to determine the material properties and the extent of deterioration.
Repair Methods for Structural Cracks
Repairing structural cracks requires careful planning and the use of appropriate methods and materials. The EN 1504 standard outlines several repair principles:
- Protection Against Ingress (Principle 1): Preventing the entry of water and other harmful agents into the structure.
- Moisture Control (Principle 2): Managing the moisture content to prevent further deterioration.
- Concrete Restoration (Principle 3): Restoring the damaged concrete to its original profile and function.
- Structural Strengthening (Principle 4): Increasing or restoring the load-bearing capacity of the structure.
- Physical Resistance (Principle 5): Enhancing the surface’s resistance to mechanical wear and tear.
Table: Typical Repair Methods and Materials
Repair Method | Description | Typical Materials |
---|---|---|
Crack Injection | Injection of low-viscosity resin into cracks to restore structural integrity. | Epoxy resins, polyurethane resins |
Surface Coatings | Application of protective coatings to prevent ingress of water and chemicals. | Acrylic coatings, epoxy coatings, silane-based sealers |
Recasting | Replacement of damaged concrete with new concrete or mortar. | High-strength concrete, polymer-modified mortar |
Cathodic Protection | Applying an electrical potential to prevent reinforcement corrosion. | Sacrificial anodes, impressed current systems |
Carbon Fiber Reinforcement | Strengthening of structural elements using carbon fiber wraps. | Carbon fiber fabric, epoxy adhesive |
Hydrophobic Impregnation | Treatment of the concrete surface to reduce water absorption. | Silanes, siloxanes, silicone emulsions |
Process of Structural Crack Repair
Below is a flow chart that outlines the typical process for assessing and repairing structural cracks:
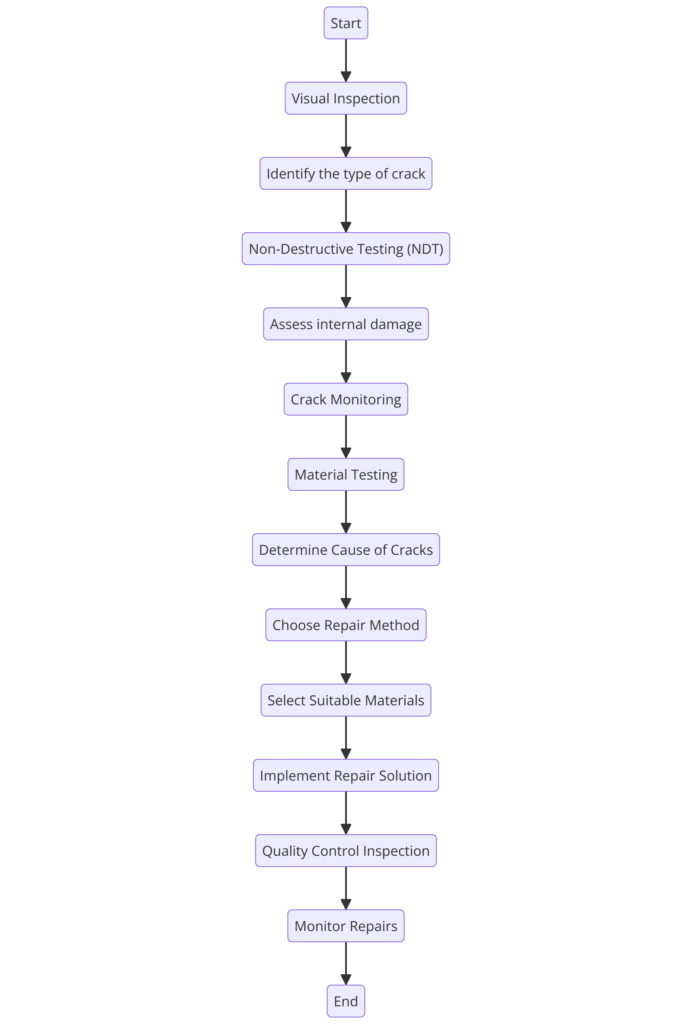
Conclusion
Structural cracks in buildings are a serious issue that requires prompt and appropriate action. By understanding the types and causes of cracks, conducting a thorough assessment, and applying the correct repair methods, you can restore the integrity of the structure and prevent further damage. Adhering to the principles outlined in EN 1504 ensures that repairs are not only effective but also compliant with international standards.
By using the right materials and techniques, you can address the root causes of structural cracks, safeguard the building’s longevity, and maintain its safety for occupants. Whether you’re a property owner, a contractor, or an engineer, staying informed and prepared is the key to effectively managing structural damage in buildings.
Contact Us for Professional Inspection Services in Malaysia
At Pro Inspect Solution, we pride ourselves on offering comprehensive inspection services to meet your property needs. Whether you require a detailed building inspection, a thorough property inspection for both residential house and commercial properties, or specialized services like pemeriksaan bangunan berkala, non-destructive testing and structural assessments, our team of experts is here to assist you.
Why Choose Us?
- Experienced Inspectors: Our inspectors are highly trained professionals with extensive experience in the industry.
- Comprehensive Reports: We provide detailed inspection reports that are easy to understand, helping you make informed decisions.
- Cutting-Edge Technology: We utilize the latest tools and techniques to ensure the highest accuracy in our inspections.
- Customer Satisfaction: Your satisfaction is our top priority, and we are committed to providing excellent service every step of the way.
Get in Touch with Us
Ready to schedule your inspection or have questions about our services? We’re here to help. Contact us today to discuss your specific needs or to get a quote.
How to Reach Us: